La digitalización está cambiando la forma en que diseñamos y automatizamos las máquinas. Solo un enfoque holístico de automatización producirá una competitividad sostenible en la nueva era de fabricación digital. Los usuarios de automatización buscan una administración de datos consistente, estándares globales, validaciones virtuales e interfaces uniformes para hardware y software. Para aquellos que están en el camino hacia la próxima generación de fabricación, el sistema SCADA actúa cada vez más como el pegamento que ayuda a unir los diferentes elementos de la empresa digital y ofrece el rendimiento deseado por los fabricantes y sus clientes.
La transformación digital abarca todos los aspectos de la sociedad, desde cómo vivimos nuestras vidas hasta cómo las empresas llevan a cabo sus negocios. El mundo nunca estuvo tan conectado; la creciente convergencia de los mundos físico y virtual ofrece oportunidades ilimitadas en casi todas las áreas de actividad. A medida que este desarrollo continúa, los fabricantes de todo el mundo están invirtiendo en las últimas tecnologías para enfrentar desafíos críticos, a saber:
- Aumento de la capacidad de producción y la flexibilidad para satisfacer la demanda en constante cambio e impulsar las ventas.
- Mejorar los niveles de calidad del servicio al cliente y reducir los costos de producción.
- Mejorar el posicionamiento competitivo agilizando la innovación, mejorando la calidad del producto y ampliando las carteras de productos y servicios.
- Optimización de la eficacia, control de costos y agilidad de fabricación mediante la automatización y la digitalización.
Los datos son la nueva materia prima, esencial en todas las áreas de la empresa, desde la investigación y desarrollo hasta la ingeniería, la logística de entrada, la producción, las ventas y la logística de salida, el mantenimiento y los servicios. Racionalizar el flujo de información a través de estas áreas y vincularlo junto con un enfoque de automatización holística es una prioridad para los líderes de fabricación actuales. Con ese fin, Siemens ha desarrollado una cartera de productos y servicios para ayudar a los fabricantes a alcanzar ese objetivo. Abordan la ingeniería integrada, la gestión de datos industriales, la comunicación industrial, la seguridad industrial y la seguridad integrada. ¿Cuál es el papel del sistema de control de supervisión y adquisición de datos (SCADA) para asegurar el funcionamiento eficiente de todos los componentes de automatización? Es crítico tomar la información de la planta y hacerla inteligente y accionable a través de la empresa digital. Como tal, el SCADA es el pegamento para el internet industrial de las cosas (IIoT), ayudando a asegurar que la información digital se comunique correctamente para hacer su trabajo en vista a un interés de digitalización industrial. ¿Por qué es importante esto? Entre las principales razones: potenciar las decisiones informadas para la planta, desde el campo hasta los niveles de gestión; transparencia energética; proporcionar informes hechos a medida en toda la empresa, y permitir una rápida identificación, locación y resolución de errores. Al proporcionar una visualización potente, el SCADA trabaja mano a mano con herramientas de ingeniería tales como TIA Portal para brindar transparencia, aumentar la productividad y lograr la digitalización. Por lo tanto, es un componente central en la realización del viaje digital a Industria 4.0.
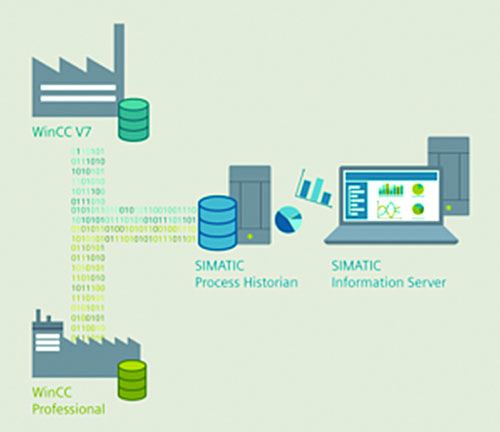
Las cinco áreas
La empresa digital actual debe tener en cuenta cinco áreas principales de actividad para lograr una digitalización efectiva:
- Gestión de datos
- Gestión de la información
- Gestión de la energía
- Gestión de diagnósticos
- Comunicación abierta
Gestión de datos
Tener datos consistentes a través de todo el proceso de producción es la base para el funcionamiento transparente de una planta y el logro de la empresa digital. La gestión de datos es esencial. La gestión inteligente incluye un alto rendimiento y un archivado fiable de datos de producción y recetas, así como la interconexión con sistemas empresariales de nivel superior (por ejemplo, ERP, MES), accesibles centralmente con un historiador de procesos. El registro de gestión de datos incluye tres elementos: registro de PLC, registro de SCADA y el historiador de proceso.
- Registro de PLC: archivado de rendimiento; acceso remoto, y administración eficiente.
- Registro SCADA: archivado de rendimiento; transparencia completa, y reconocer tempranamente las tendencias.
- Historiador de proceso: cantidad ilimitada de datos; archivamiento eficiente, y conexión de sistemas externos.
Dentro de la gestión de datos, el SCADA es en tiempo real y local, mientras que el historiador de proceso es a largo plazo y global. En conjunto, empoderan las decisiones sobre una base empresarial.
Gestión de la información
La gestión de la información potencia la producción transparente para procesos optimizados, lo cual permite que se tomen las decisiones correctas al instante. Sus herramientas incluyen:
- informes y controles basados en la web;
- análisis específico de grupo de datos de producción con un servidor de información;
- control y monitoreo basado en la web, flexible en diversos dispositivos y navegadores y acceso remoto completo;
- control remoto de las estaciones de trabajo;
- acceso basado en navegador para: comunicación óptima de la información, información segura y facilidad de uso;
- funcionamiento coordinado de múltiples estaciones, y
- configuración cliente/servidor para soluciones.
Gestión de la energía
La gestión de la energía proporciona transparencia energética para el ahorro de energía, de acuerdo con ISO 50001. Esta área resulta de creciente preocupación en Estados Unidos. Las herramientas para realizar un seguimiento de la gestión de la energía deben permitir un registro fácil y eficiente de los datos y facilitar la reducción de los costos operativos a través de un sistema integral de gestión.
- Sistema de gestión de la energía que proporcione control de eficiencia energética, centros de costo, e informes y dashboards.
- Software de monitoreo de energía que proporciona generación automática de herramientas de PLC para adquisición y procesamiento de energía.
El software se configura fácilmente debido a la integración en el software de ingeniería y proporciona la realización eficiente a través de la generación automática del programa de energía. El software se conecta perfectamente al sistema de gestión de energía y respeta el cumplimiento de los requisitos legales. (Está diseñado para hacerlo de forma automática, pero los parámetros se pueden modificar manualmente en el TIA Portal).
Gestión de diagnósticos
La gestión de diagnósticos ayuda a aumentar la disponibilidad de máquinas y plantas de producción. A través del TIA Portal, los diagnósticos se pueden examinar y poner en el sistema SCADA, permitiendo un seguimiento y una corrección de las excepciones más rápido. Entre sus beneficios:
- Revisión simple de la información del sistema debido al acceso rápido al estado de diagnóstico de todos los dispositivos.
- Alarmas de diagnóstico para cortocircuitos, rotura de cables, cargas de voltaje perdidas, limitaciones de violaciones, etc.
- Visualización uniforme en todos los dispositivos (PLC, HMI local, SCADA y servidor web).
- Identificación rápida de errores que muestran la operación defectuosa directamente en la notificación.
- Corregir errores rápidamente con información clara sobre la localización, causa y solución de problemas.
- Servicio sin programación: visión general y diagnóstico detallado directamente en el panel de mando.
- Integrado: generación automatizada de código PLC y visualización del estado actual.
- Sin contragolpe: define supervisiones independientemente del programa de usuario.
- Siempre al día: sincronización permanente de los dispositivos operativos, incluso después de cambiar el programa de usuario.
Comunicación abierta
La comunicación abierta permite combinar automatización y TI para aprovechar todos los datos de producción relevantes. Además, permite una integración fácil de sistemas de nivel superior, como MES y ERP. La compatibilidad con el protocolo de comunicación estandarizado OPC UA permite la conexión de sistemas de proveedores cruzados. Esto proporciona: fácil integración y ampliación con OPC UA y ProfiNet LAN; amplia comunicación a través de OPC UA en PLC modernos y software de sistema SCADA, y autenticación y cifrado que garantizan una comunicación coherente y segura. La comunicación de datos entre sistemas se realiza a través de interfaces estándar con un puente de datos industriales (IDB, por su sigla en inglés). Esto permite: transferencia bidireccional de datos entre sistemas a través de interfaces estándar; transmisión fiable y segura mediante el uso de parametrización en lugar de programación, y aplicabilidad universal como servicio del sistema o como opción integrada del sistema SCADA.
La información de todos los dispositivos se alimenta en el sistema SCADA. Para cada requisito del cliente, existe un beneficio del SCADA correspondiente. El SCADA reside en los niveles funcionales 1 y 2 de una operación de control de fabricación. Al unir esencialmente las cinco áreas, actúa como pegamento para la digitalización, facilitando la información a través de procesos más rápidos, desde la planta hasta los niveles más altos de gerencia. |