En este artículo, una presentación de algunos de los trabajos finales elaborados por personal ingenieril de YPF Upstream en el marco del posgrado de Especialización en Automatización Industrial de la Facultad de Ingeniería de la Universidad de Buenos Aires
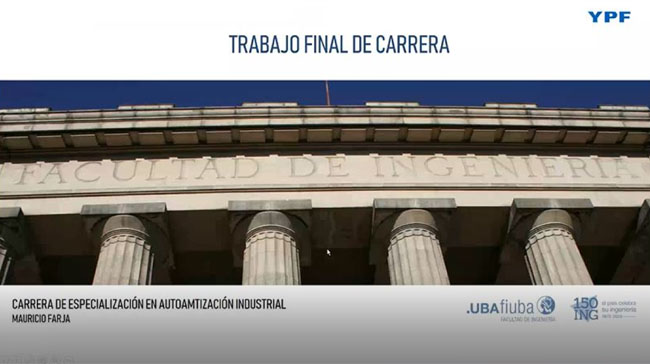
La carrera de Especialización en Automatización Industrial es un posgrado profesional de la Facultad de Ingeniería de la Universidad de Buenos Aires (FIUBA) que se cursa en tres cuatrimestres. Durante el periodo lectivo 2019-2020 tuvo una implementación particular: por un convenio entre YPF y FIUBA, se dictó para un grupo formado exclusivamente por ingenieros e ingenieras de YPF Upstream. La experiencia resultó muy interesante y productiva, tanto para el personal técnico de YPF como para los docentes e investigadores de FIUBA.
La carrera de Especialización en Automatización Industrial es un posgrado profesional de la Facultad de Ingeniería de la Universidad de Buenos Aires (FIUBA) que se cursa en tres cuatrimestres.
Según el plan de la especialización, después de completar las materias de los tres cuatrimestres, el alumnado debe preparar y defender un trabajo final para obtener su título. El objetivo es integrar lo aprendido con alguna problemática del ambiente laboral en el que se desenvuelve cada estudiante. Para este último ciclo de cursos, debido a la cuarentena vigente, la exposición de los trabajos finales fue virtual, ante el tribunal y una numerosa presencia de interesados.
A continuación, un panorama de los trabajos de los seis primeros graduados y graduadas en el marco de este convenio UBA-YPF da una idea de lo fructífera que fue esta experiencia.
A continuación, un panorama de los trabajos de los seis primeros graduados y graduadas en el marco de este convenio UBA-YPF da una idea de lo fructífera que fue esta experiencia.
“Reducción del riesgo de la maniobra de desarenado mediante su automatización”, de Micaela Villaola
Planteo del problema
En las instalaciones de superficie de la operación no convencional de gas (upstream), suele incluirse un equipo llamado “desarenador”, que se encarga de separar los sólidos asociados a los procesos de fractura típicos de esta operación, que se extraen en conjunto con el petróleo, el gas y el agua del subsuelo. Los sólidos que se acumulan en el equipo se deben remover periódicamente con el objetivo de garantizar la operación eficiente, mediante la maniobra de desarenado. Esta maniobra consta de una serie de etapas: 1) bypass del equipo; 2) aislamiento del equipo; 3) despresurización desde la presión de operación (aproximadamente 80 kgf/cm2) a aproximadamente 10 kgf/cm2; 4) Purga, barriendo los sólidos con los 10 kgf/cm2 de presión remanente en el equipo hacia la cámara de arena, y 5) normalización de la operación.
Durante un relevamiento sobre la instalación, se advirtió sobre el riesgo significativo de esta maniobra manual. A partir de la necesidad de reducir el riesgo de la maniobra de desarenado, se busca dar solución desde el campo de la automatización, de forma tal que se aleje a la persona del lugar y que la maniobra se pueda hacer desde sala de control con la supervisión del operador.
Durante un relevamiento sobre la instalación, se advirtió sobre el riesgo significativo de esta maniobra manual. A partir de la necesidad de reducir el riesgo de la maniobra de desarenado, se busca dar solución desde el campo de la automatización, de forma tal que se aleje a la persona del lugar y que la maniobra se pueda hacer desde sala de control con la supervisión del operador.
Objetivos
- Objetivo general: realizar un diseño automatizado del sistema que permita reducir el riesgo de la maniobra de desarenado.
-
Objetivos específicos:
-
relevar la maniobra de desarenado actual;
- cuantificar el riesgo de la maniobra de desarenado actual;
- definir una arquitectura automatizada del sistema que permita reducir el riesgo actual: definición de la instrumentación básica necesaria y qué válvulas requerirán actuadores para automatizar la maniobra;
- desarrollar el diagrama lógico de la maniobra de desarenado automatizada, de acuerdo a Norma ISA 5.2.;
- verificar su funcionamiento a través de una simulación realizada en el entorno Matlab/Simulink, para lo que es necesario realizar un modelo matemático del proceso;
- seleccionar de forma multidisciplinaria los elementos necesarios para el automatismo;
- confirmar la reducción de riesgo en el caso de incorporar la propuesta, a través de un nuevo estudio de riesgo residual;
- realizar un modelo de dispersión de la mezcla explosiva para verificar el radio de alcance, de forma tal de abordar el riesgo residual.
Dado que existen otras instalaciones de no convencional, y considerando la proyección que tienen este tipo de yacimientos en nuestro país (formación Vaca Muerta), se vislumbra la posibilidad de extrapolar los resultados obtenidos a otras instalaciones.
“Optimización del automatismo en un sistema de transferencia de agua de inyección”, de Mauricio Farja
Problemática planteada
El sistema de transferencia de agua de inyección desde la planta de tratamiento de aguas a las plantas de inyección en el yacimiento Barrancas (en Mendoza) está compuesto por dos bombas centrífugas, cada una de las cuales cuenta con una válvula de control neumático que regula la presión de impulsión. Las líneas de impulsión de las dos bombas se unifican en un ducto troncal que luego se divide en tres líneas de transferencia. Se plantea la necesidad de optimizar la instalación para poder controlar el caudal transferido en cada una de las tres líneas.
Solución con control y automatización
El proyecto presentado optimiza el sistema de transferencia sumando funciones al sistema de control del proceso. Requiere implementar cuadros de control en cada una de las líneas de transferencia y que se autorregulen en función de los caudales configurados por la operación. Los cuadros de control de presión se deshabilitan mientras operan los lazos de caudal, evitando la competencia de lazos, dejando el control por presión como lazo de control de respaldo. Como parte central del trabajo, se analizaron distintas alternativas: control con recirculación, incorporando una válvula de recirculación a tanque; control con variador de velocidad, que se desestima; control PID, a partir de los elementos ya instalados. Adicionalmente, se desarrollaron las pantallas del sistema SCADA desde donde el operador comandará el sistema de transferencia de agua. Como resultado se obtuvieron controles de caudal independientes operando en forma simultánea y con la aplicación de un control override para un control de sobrepresión de los ductos. Para la sintonía de los lazos y análisis de implementación, se utilizaron rampas de arranque, ajuste de tiempo y se realizaron las modelizaciones matemáticas de cada sistema y su correspondiente simulación en Simulink.
“Diseño de una estrategia de control para evitar desvíos de presión durante la laminación de gas”, por Pablo Morales
A medida que un yacimiento se desarrolla, se instalan en pozos sistemas de extracción artificial tales como bombeo mecánico, bombeo electrosumergible, plunger lift o compresores de boca de pozo, entre otros. Una vez en superficie, el fluido se transporta a las unidades primarias de tratamiento: el petróleo a las baterías y el gas, a las unidades de separación primaria (USP). Allí se realizan separaciones líquido/gas y líquido/líquido, se miden las fases, se contabiliza la producción total y se envía el producto a las respectivas plantas de tratamiento. Si el gas tiene menos presión de la requerida, primero se envía a una estación compresora, que cuenta con máquinas de desplazamiento positivo o compresores alternativos reciprocantes en los que, por medio de un pistón, se eleva la presión de sucesivos volúmenes de gas hasta un valor determinado.
Planteo del problema
Una estación compresora de YPF cuenta con dos máquinas que reciben gas a baja presión (4 kg/cm2). Allí comprimen el gas hasta 68 kg/cm2. Si las variables de operación del compresor se encuentran por fuera de la ventana operativa, este detiene su marcha para evitar recalentamientos o roturas internas.
La instalación cuenta con una acometida que une un sistema de media presión (8 kg/cm2) con uno de baja presión para suplir una falta de caudal. La estrategia de control actual consta de dos válvulas neumáticas instaladas en cada línea que comparten un mismo controlador. La medición de presión y su transmisión se hace por medio del PIT 100 que se encuentra sobre la succión.
Este proceso en el cual se compensa la caída de presión de un sistema con otro es lo que se conoce como “laminación de gas”, situación no deseable y totalmente ineficiente.
Con la configuración actual, a medida que la presión de succión disminuye por el cierre de alguna línea de producción, la laminación resulta abrupta y no permite sintonizar las velocidades de reacción de las válvulas correctamente.
La instalación cuenta con una acometida que une un sistema de media presión (8 kg/cm2) con uno de baja presión para suplir una falta de caudal. La estrategia de control actual consta de dos válvulas neumáticas instaladas en cada línea que comparten un mismo controlador. La medición de presión y su transmisión se hace por medio del PIT 100 que se encuentra sobre la succión.
Este proceso en el cual se compensa la caída de presión de un sistema con otro es lo que se conoce como “laminación de gas”, situación no deseable y totalmente ineficiente.
Con la configuración actual, a medida que la presión de succión disminuye por el cierre de alguna línea de producción, la laminación resulta abrupta y no permite sintonizar las velocidades de reacción de las válvulas correctamente.
Desarrollo del trabajo
Un control feedback es la estrategia apropiada para resolver la problemática. La PV 100ª debe quedar abierta y en un futuro ser retirada de la instalación. La válvula PV 100B debe reemplazarse por una de menor tamaño.
Se utiliza la herramienta Simscape para representar el sistema, ya que permite crear sistemas físicos dentro del entorno de Simulink.
Se simula un conjunto de pozos a 4 kg/cm2 de presión junto a una válvula globo que realiza el cierre programado, restringiendo el caudal de gas. La disminución de caudal genera pérdida de presión en el sistema.
Cuando la presión cae por debajo del punto de configuración, el PID envía una señal de apertura a la válvula de control que se encuentra en una cañería con gas a 8 kg/cm2, laminando el gas que se dirige a los compresores.
La apertura de la válvula de control 4” es cercana al 24%. Se propone utilizar una válvula de 2”, lo que genera por simulación un valor de 51% de apertura.
Se utiliza la herramienta Simscape para representar el sistema, ya que permite crear sistemas físicos dentro del entorno de Simulink.
Se simula un conjunto de pozos a 4 kg/cm2 de presión junto a una válvula globo que realiza el cierre programado, restringiendo el caudal de gas. La disminución de caudal genera pérdida de presión en el sistema.
Cuando la presión cae por debajo del punto de configuración, el PID envía una señal de apertura a la válvula de control que se encuentra en una cañería con gas a 8 kg/cm2, laminando el gas que se dirige a los compresores.
La apertura de la válvula de control 4” es cercana al 24%. Se propone utilizar una válvula de 2”, lo que genera por simulación un valor de 51% de apertura.
Conclusiones
Al no contar con la función de transferencia del sistema, la simulación en Simscape representa el sistema y su comportamiento antes y luego del control.
No resulta necesario modular la válvula PV 100A para poder controlar las perturbaciones de presión en el scrubber de succión del compresor, por lo que el controlador PIC 100 solo debe intervenir con la PV 100B y se debe dejar abierta al 100% la PV 100A.
Se recomienda el cambio de válvula de control por una de 2”.
El control feedback resulta ser la estrategia correcta para evitar la detención de los compresores por baja presión de succión.
No resulta necesario modular la válvula PV 100A para poder controlar las perturbaciones de presión en el scrubber de succión del compresor, por lo que el controlador PIC 100 solo debe intervenir con la PV 100B y se debe dejar abierta al 100% la PV 100A.
Se recomienda el cambio de válvula de control por una de 2”.
El control feedback resulta ser la estrategia correcta para evitar la detención de los compresores por baja presión de succión.
“Modelado para el ajuste de control de bombas con variador”, por Pablo Prieto
Problemática planteada
La propuesta está basada en el parque de bombas de la planta de inyección de agua “Mari Menuco” (PIA MM), ubicada en el yacimiento Sierra Barrosa, en la provincia de Neuquén. Esta cuenta con cuatro bombas encargadas de abastecer de agua para recuperación secundaria a la planta de tratamiento de crudo Aguada Toledo (PTC AT). Actualmente, la demanda ha disminuido al punto de que el abastecimiento se puede realizar con solo una bomba e, incluso, la mayoría del tiempo, su capacidad excede la demanda.
Solución con control y automatización
El sistema posee un variador de velocidad que originalmente se utilizaba como un arranque suave para luego dejar las bombas conectadas de forma directa a la frecuencia de la red en las épocas de mayor consumo, y evitar así perturbaciones significativas en la red eléctrica del yacimiento. El variador está diseñado para operar con una carga cuya potencia es equivalente a la de una de las bombas del parque de PIA MM (600 HP).
Se plantea realizar el ajuste de los lazos de control del sistema de bombeo de despacho de agua para lograr una operación estable con respuesta efectiva ante los cambios de demanda de caudal, operando además con el menor consumo de energía posible, mediante el control de velocidad combinado con la acción de las válvulas de recirculación y salida de planta que se hacía originalmente.
El trabajo presentado plantea elaborar el modelo matemático que representa el sistema de bombeo de forma integral, incluyendo las ecuaciones características de las válvulas de recirculación y salida de planta, y la de la curva de la bomba en función del caudal y presión, con la particularidad de que los coeficientes de los términos cuadrático, lineal e independiente se expresan en función de la velocidad del eje. Al modelo se le agregan las ecuaciones correspondientes a un controlador PID, utilizando solo las constantes proporcional e integral.
Una vez que se completó el modelo para la simulación en lazo cerrado mediante el software Simulink, se utilizaron dos metodologías de ajuste, Zieggler-Nichols e IMC, para hallar las constantes del controlador. El mejor resultado se obtuvo mediante la implementación de un controlador IMC. Las perturbaciones de gran intensidad fueron absorbidas de forma adecuada aun cuando la condición de consumo de agua en el acueducto era de baja.
Se plantea realizar el ajuste de los lazos de control del sistema de bombeo de despacho de agua para lograr una operación estable con respuesta efectiva ante los cambios de demanda de caudal, operando además con el menor consumo de energía posible, mediante el control de velocidad combinado con la acción de las válvulas de recirculación y salida de planta que se hacía originalmente.
El trabajo presentado plantea elaborar el modelo matemático que representa el sistema de bombeo de forma integral, incluyendo las ecuaciones características de las válvulas de recirculación y salida de planta, y la de la curva de la bomba en función del caudal y presión, con la particularidad de que los coeficientes de los términos cuadrático, lineal e independiente se expresan en función de la velocidad del eje. Al modelo se le agregan las ecuaciones correspondientes a un controlador PID, utilizando solo las constantes proporcional e integral.
Una vez que se completó el modelo para la simulación en lazo cerrado mediante el software Simulink, se utilizaron dos metodologías de ajuste, Zieggler-Nichols e IMC, para hallar las constantes del controlador. El mejor resultado se obtuvo mediante la implementación de un controlador IMC. Las perturbaciones de gran intensidad fueron absorbidas de forma adecuada aun cuando la condición de consumo de agua en el acueducto era de baja.
“Automatización y control de un separador bifásico vertical”, por Gustavo Robledo
Problemática planteada
Las mediciones en campo son de vital importancia para la determinación confiable de la producción. Tener una forma sistematizada de medir esta producción ayuda a la toma de decisiones en los proyectos de inversión de la compañía.
En un el campo petróleo, el recuento de la producción es una de las tareas fundamentales y que más tiempo puede llevar a los operarios. Esta tarea es la que cierra el número final en inversiones en los distintos negocios, por lo que tener una metodología que disminuya la incertidumbre que conlleva cualquier medición sería de utilidad en la decisión final.
En un el campo petróleo, el recuento de la producción es una de las tareas fundamentales y que más tiempo puede llevar a los operarios. Esta tarea es la que cierra el número final en inversiones en los distintos negocios, por lo que tener una metodología que disminuya la incertidumbre que conlleva cualquier medición sería de utilidad en la decisión final.
Solución con control y automatización
El objetivo principal del proyecto planteado es especificar instrumentos y equipos necesarios, junto con las estrategias de control, para que los separadores de control instalados en campo puedan realizar la medición y control del pozo de forma automática, utilizando los equipos disponibles y considerando la capacidad de mantener las funciones con los recursos de la zona.
Como base del diseño se tomó un separador bifásico vertical de control de 200 m3/día junto con sus pozos.
El proyecto tiene dos aristas marcadas: por un lado, se trabajó en la instrumentación y por el otro, en el control del lazo de nivel necesario para el correcto funcionamiento del separador.
Para la instrumentación, se especificaron cada uno de los equipos.
Ya sea para instrumentos ya presentes como para equipos nuevos, se tuvo en cuenta el historial de fallas, la adquisición y el conocimiento de los operarios en campo, tanto de producción, para su utilización, como los operarios de mantenimiento, para la ejecución de las rutinas preventivas.
Para el control automático del nivel del separador, con el software Simulink, se construyó el modelo del separador mediante bloques. Finalmente, se puede obtener un modelo completo del sistema, con sus perturbaciones (caudal de ingreso, presión del separador y presión de descarga del separador).
Se escoge para el ajuste del lazo, una estrategia por IMC con rechazo de perturbaciones.
Como base del diseño se tomó un separador bifásico vertical de control de 200 m3/día junto con sus pozos.
El proyecto tiene dos aristas marcadas: por un lado, se trabajó en la instrumentación y por el otro, en el control del lazo de nivel necesario para el correcto funcionamiento del separador.
Para la instrumentación, se especificaron cada uno de los equipos.
Ya sea para instrumentos ya presentes como para equipos nuevos, se tuvo en cuenta el historial de fallas, la adquisición y el conocimiento de los operarios en campo, tanto de producción, para su utilización, como los operarios de mantenimiento, para la ejecución de las rutinas preventivas.
Para el control automático del nivel del separador, con el software Simulink, se construyó el modelo del separador mediante bloques. Finalmente, se puede obtener un modelo completo del sistema, con sus perturbaciones (caudal de ingreso, presión del separador y presión de descarga del separador).
Se escoge para el ajuste del lazo, una estrategia por IMC con rechazo de perturbaciones.
“Software de identificación de modelos y diseño de controladores”, por Héctor Sifon
Durante el desempeño diario del ingeniero de control, suele ser necesario realizar ajustes de lazos PID, usualmente en situaciones donde no se dispone de modelo dinámico de la planta, y muchas veces, tampoco del tiempo para su obtención. Producto de esto, la mayor parte del trabajo de ajustes de lazos de control se realiza prescindiendo de las herramientas analíticas ampliamente conocidas y muy efectivas. A los efectos de salvar esta problemática, se planteó como objetivo del trabajo el desarrollo de un software de asistencia para la identificación de modelos y ajuste de lazos de control. La herramienta obtenida como resultado de este trabajo permite identificar los parámetros del modelo, cuyo orden es definido por el usuario, a partir de la importación de datos de una prueba del tipo “Bump test” realizada sobre el lazo de control.
Para la identificación de parámetros se utilizó el método de estimación por mínimos cuadrados, a lo que se adicionó una etapa de ajuste final por método de descenso de gradiente. Esta última etapa permite corregir los casos donde, por presencia de ruido de medición, se obtengan parámetros con sesgo de estimación, lo cual es inherente al método de mínimos cuadrados.
Cabe mencionar que, al considerar como punto de partida para el algoritmo de descenso de gradiente, la estimación obtenida por mínimos cuadrados, se elude la problemática de mínimos locales que puede suceder si se utiliza el método de descenso de gradiente por sí solo. Con esta combinación en etapas de algoritmos, se ha obtenido un buen desempeño en la estimación de parámetros de modelos aún en condiciones de señales ruidosas.
Adicional a la funcionalidad de identificación de modelo, el software desarrollado posee un entorno de simulación, el cual permite verificar el comportamiento a lazo cerrado para distintas configuraciones del controlador, siendo posible verificar el desempeño ante perturbaciones y cambios de “set point”. Por otra parte, la herramienta puede también obtener la configuración del controlador por método de IMC y calcular la distancia entre el gráfico de Nyquist al punto crítico, lo que da una idea de la robustez del ajuste realizado sobre el PID; logrando así un conjunto de funcionalidades que resulta muy útil como herramienta de apoyo en la tarea diaria del ingeniero de control.
Para la identificación de parámetros se utilizó el método de estimación por mínimos cuadrados, a lo que se adicionó una etapa de ajuste final por método de descenso de gradiente. Esta última etapa permite corregir los casos donde, por presencia de ruido de medición, se obtengan parámetros con sesgo de estimación, lo cual es inherente al método de mínimos cuadrados.
Cabe mencionar que, al considerar como punto de partida para el algoritmo de descenso de gradiente, la estimación obtenida por mínimos cuadrados, se elude la problemática de mínimos locales que puede suceder si se utiliza el método de descenso de gradiente por sí solo. Con esta combinación en etapas de algoritmos, se ha obtenido un buen desempeño en la estimación de parámetros de modelos aún en condiciones de señales ruidosas.
Adicional a la funcionalidad de identificación de modelo, el software desarrollado posee un entorno de simulación, el cual permite verificar el comportamiento a lazo cerrado para distintas configuraciones del controlador, siendo posible verificar el desempeño ante perturbaciones y cambios de “set point”. Por otra parte, la herramienta puede también obtener la configuración del controlador por método de IMC y calcular la distancia entre el gráfico de Nyquist al punto crítico, lo que da una idea de la robustez del ajuste realizado sobre el PID; logrando así un conjunto de funcionalidades que resulta muy útil como herramienta de apoyo en la tarea diaria del ingeniero de control.
Por Carlos Godfrid
Autor:
Publicado en:
Número:
Mes:
Año: